Table of Contents
What is modular construction?
Modular Integrated Construction (MiC) It is an innovative construction technology that significantly improves efficiency and quality by prefabricating modular components in the factory and quickly assembling them on site. Here are its key points:
1. Definition and core concepts
- Modular Integration: Break down the building into independent functional modules (such as rooms, bathrooms), complete the structure, decoration, water and electricity processes in the factory, and transport them to the construction site for assembly like "building blocks".
- Full process integration:Combining design, manufacturing, logistics and construction, emphasizing the coordination of all links (such as using BIM technology to ensure accuracy).
2. Process steps
- Design Phase: Use BIM for modular design and optimize size and interfaces.
- Factory prefabrication: Modules are produced in a controlled environment to ensure consistent quality.
- Logistics and transportation: The module size must comply with transportation restrictions (such as container size).
- On-site assembly: Hoisting modules and connecting water, electricity and structure can greatly shorten the construction period.
3. Core advantages
- Improved efficiency:Shorten construction time on site by 30%-50%, especially suitable for projects with tight deadlines.
- Quality control:The factory environment reduces human errors and improves waterproofing, sound insulation and other performances.
- Environmental protection and energy saving: Reduce construction site waste, noise and carbon emissions, and support green building certification (such as LEED).
- High security: Reduce high-altitude operations and the number of workers on site to reduce the risk of accidents.
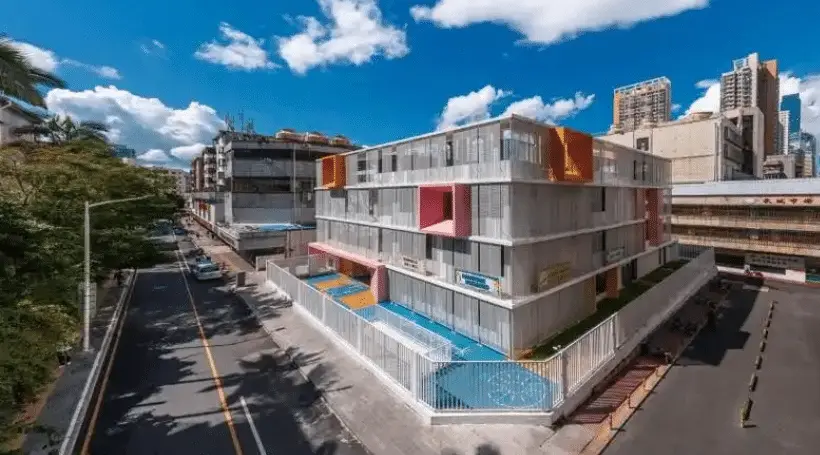
4. Typical application scenarios
- High-density residential: Such as Hong Kong’s public housing project, which quickly solves the housing shortage.
- Medical and educational facilities: Quickly build isolation wards or school buildings during an epidemic.
- Commercial Space:Hotels and office buildings use modular repetitive design to reduce costs.
5. Challenges and limitations
- High upfront costs: Investment in factories and supply chains is required, and small projects may not be economical.
- Design Flexibility: The module size is limited by transportation, and special-shaped buildings are difficult to realize.
- Logistical complexity: The transportation of large modules requires special route planning and coordination with traffic control.
6. Actual Cases and Policies
- Hongkong:The government has listed MiC as a priority for "innovative construction" for use in transitional housing and public housing, with the goal of shortening construction periods by one-third.
- Singapore:Promote the "Easy Build" plan and encourage prefabricated module technology.
- Mainland: Shenzhen, Shanghai and other places have applied MiC in talent apartment projects, achieving "building one floor in 7 days".
優缺點分析-1.webp)
7. advantage
Shorten your stay
Factory prefabrication and on-site construction are carried out simultaneously, which greatly shortens the overall construction period (can be shortened by 30-50%), allowing users to move in or use the space faster, which is especially suitable for situations where housing or commercial facilities are urgently needed.
Stable and controllable quality
Produced in a factory environment, defects caused by weather or human error are reduced, and the module's structure, waterproofing, sound insulation and other qualities are more consistent, reducing the need for subsequent maintenance.
High cost predictability
Standardized factory production helps control budgets, reduces additional costs common in traditional construction, and is more beneficial to the financial planning of owners or investors.
8. shortcoming
Limited design flexibility
The module size is subject to transportation restrictions (such as road width), and the interior layout and exterior design may be more standardized, making it difficult to meet highly customized needs.
Initial costs may be higher
Factory production and transportation costs may be higher than traditional methods, especially in small projects, where the cost advantage is less obvious and may be passed on to users when purchasing a home or renting it.
Maintenance and renovation challenges
If problems occur at the joints of the modules (such as water leakage or structural displacement), professional technical repairs are required; subsequent expansion or renovation may also be complicated by the modular structure.
Market acceptance and resale concerns
Some users have doubts about the durability or value retention of prefabricated buildings, which may affect the market value of real estate and it will take time to build trust.
Transportation and site restrictions
The transportation of large modules requires special permits, and the cost is increased in remote areas or places with inconvenient transportation; there must also be enough space on site to place and hoist the modules.
Further reading:
- Modular Integrated Construction Buildings Departmentmaterial
- Modular Integrated Construction wiki
- Hong Kong Housing Society's "Jun Ran" and "Ju Ran" application qualifications